-
Rubber Process Machine
-
Rubber Mixing Mill Machine
-
Rubber Powder Production Line
-
Rubber Kneader Machine
-
Rubber Banbury Mixer
-
Rubber Vulcanizing Press
-
Reclaimed Rubber Sheet Line
-
Plastic Recycling Line
-
Tennis Ball Making Machine
-
Rubber Grinder Machine
-
Batch Off Rubber Cooling Machine
-
Rubber Conveyor Belt Production Line
-
Rubber Calender Machine
XK-550 Rubber Mixing Mill Machine 110Kw Open Mill Rubber Mixing
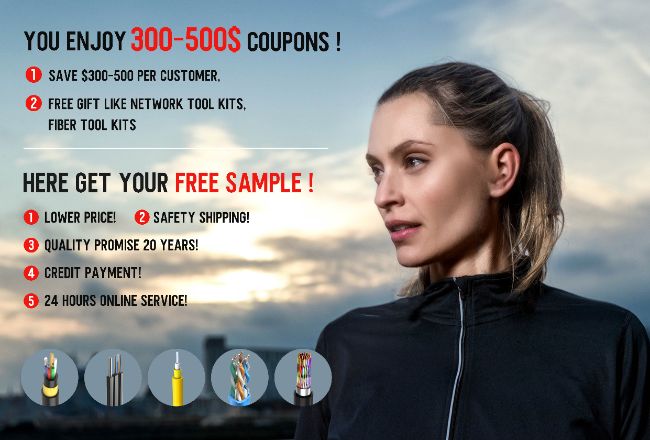
Contact me for free samples and coupons.
whatsapp:0086 18588475571
wechat: 0086 18588475571
skype: sales10@aixton.com
If you have any concern, we provide 24-hour online help.
xDiameter Of Roll(mm) | 550 Mm | Length Of Roll(mm) | 1530 Mm |
---|---|---|---|
Video Outgoing-inspection | Provided | Machinery Test Report | Provided |
Condition | New | Warranty | 1 Years |
Key Selling Points | Long Service Life | Applicable Industries | Rubber Plastic Industry |
Machine Type | Rubber Mixing Mill Machine | Roller Hardness | Chilled Cast Iron Hardness HS 72 |
Highlight | XK-550 Rubber Mixing Mill Machine,Rubber Mixing Mill Machine 110Kw,ISO Open Mill Rubber Mixing |


Plus one plate of plane thrust bearing,each mill has 12 plates of bearing,saving energy by 10-15% and reducing grease usage by 20-25%




Factory Direct Sales Rubber Mixing Mill Machine Open Mixing Mill Machine For Rubber Processing
Equipment application and operation requirements
1.1 Main application: mixing mill is mainly used for rubber compound warming, mixing &sheeting, as well as raw rubber plasticating, mixing &sheeting.
1.2 Operation requirements A. running environment: altitude<1000m,
temperature: 5℃-40℃, max. relative humidity 95%
B. Power supply: AC380V, 50Hz, 3-phase
C. Cooling water pressure: 0.2-0.4Mpa
Cooling water temperature: ﹤25℃±3℃
2 Main technical parameters
Roll diameter 550mm
Roll working length 1530mm
Batch capacity 50-65kg
Front roll structure drilled roll &smooth
Rear roll structure plain roll centrally cooling
Front roll linear speed 28 or 31m/min
Speed ratio of rolls 1:1.2 or 1:1.09
Max. roll nip 16mm
Main motor power AC110kw
Cooling water pressure 0.2-0.4Mpa
Lubrication motorized grease pump
Stock guider type fixed or manual movable
Stock blender type motorized or hydarulic
Overall dimensions(L*W*H) 6500x2000x2300mm
Approx. weight 23000kg
3.Supply range
Main body (including bedplate, frame and rolls) 1set
Nip adjusting device and safety device 1set
Coupling 1set
Gear reducer and lubrication system 1set
Grease lubrication system 1set
Roll temperature adjusting device 1set
Emergency stop device 1set
Main motor 1set
Electrical control system 1set
Parts connection &fixing bolts 1set
Foundation bolts 1set
4 Following items prepared by end user
A. Power cables from power supply to electrical control cabinet and power cables from
electrical control cabinet to mill main motor.
B. All pipelines outside rotary joints.
5 Fabrication and technical standards
5.1 Roller: made of Nickel, Chrome &Molybdenum chilled cast iron through
centrifugal casting. Roll surface hardened layer depth is up to 10-15mm,
hardness is around HS73±2.
5.2 Roll bearing and seal: 8pcs double-row cylindrical roller bearing is adopted coupling with 4pcs more thrust bearing, 12pcs bearings for each machine, which could save energy consumption up to 10-15%, lubrication grease is reduced by 20-25%.
2sets double-row cylindrical roller bearings for each bearing house
5.3 Roll bearing lubrication: motorized auto grease pump.
5.4 Bearing house: made of cast steel or cast iron through anneal heating treatment and processing, with lubrication holes reserved.anneal heating treatment bearing houses
5.5 Nip adjusting device: motorized nip adjusting system, both single adjusting and multi-adjusting are available.
5.6 Frame: made of cast iron or fabricated through anneal heating treatment and processing.
5.7 Bedplate: integral welding structure, made of superior U steel and constructional steel through anneal heating treatment and processing.
5.8 Stock guider: fixed type.
5.9 Transmission system: complete enclosed drive, through couplings, gear reducer(single input shaft and single output shaft), driving gear and friction gear, main motor drives the two rolls relative rotating at different speed, plasticating, mixing or sheeting could be therefore realized.
5.10 Roll temperature adjusting device: consisting of superior rotary joints and stainless steel pipe with drilled spraying nozzles.
5.11 Emergency stop and braking device: energy consumption method is used to
stop the mill. There are 3-emergency stop buttons fitted on the frames, press
the button if any emergency situation occurs, the roll rotation will not exceed
1/4 circle and main motor reverse 1/4 circle thereafter within 2 seconds.
Meanwhile, this mill is fitted with electrical-hydraulic brake system, which
improves equipment safety ability significantly.
pulling rope/chest bar, foot pedal, safety protection bar are all available.
5.12 Stock pan: welded by superior stainless steel plate.
5.13 Main motor start up: Star-delta starting.
5.14 Cutter device: 2pcs manual straight cutter.
5.15 Stock blender: motorized or hydraulic type.Motorized type stock blender


Market advantage
Technical advantages
